ValCUN
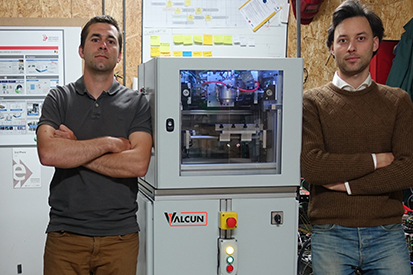
The new era of metal 3D-printing
TEXT: ARNE ADRIAENSSENS | PHOTOS © VALCUN
Though most 3D-printers use plastics, the production industry holds many opportunities for metal additive manufacturing as well. Today, however, the enormous price tag and the slow building rates prevent many companies from taking the leap. The Flemish start-up ValCUN is about to change that. They are creating an affordable and fast metal 3D-printer which delivers top-notch quality.
“In 2014, I was developing a rocket engine in my spare time,” ValCUN founder, Dr. Jonas Galle, explains. “I did everything myself: from calculating the data to creating the design, as well as the manufacturing of its components. During the milling of the complex main engine’s parts, I started to understand the benefits of metal 3D-printing. Diving deeper into it, I was shocked by how expensive the technology was. I found it hard to believe that it had to be that expensive.” Triggered by this factor, Galle started investigating the causes of such a high price and how they could be avoided or replaced. This resulted in the creation of his disruptive technology and the founding of ValCUN.
To date, most metal additive manufacturing systems use a very fine metal powder that is spread out layer per layer, and molten with a high-power laser. This method is very slow and asks for lots of unnecessary extra metal powder, an expensive product which must be stocked carefully to prevent powder explosions or people inhaling it. “We threw all of this overboard, dared to take a big step back and asked ourselves: ‘How can we make it economically competitive?’. We came up with a patent-pending technology that combines the advantages of both low-cost plastic printing (fused deposition modelling) and plasma cutting technology, and baptised our Molten Metal Deposition. We melt raw metal and extrude it through a nozzle on a preheated surface, just like a pastry chef does with molten chocolate.”
Recycled metals
ValCUN’s technology has several advantages over the existing ones. Since metal gets molten prior to printing, it is unnecessary to use expensive metal powders. Instead, you can opt for standard metal wires, raw metals or even recycled ones. You can throw old or broken parts into the machine to print brand new ones with that material. “Right now, we focus on printing with aluminium,” explains co-founder Dr. Ir. Jan De Pauw. “With its excellent heat conductivity, it can be used in many industries for cooling or heat exchange applications. Afterwards, we will adapt our printers to work with other metals as well, like copper and stainless steel, for example. We also want to collaborate with our clients to discover what their needs are and start from there.”
Another advantage of ValCUN’s printer is its speed, which is significantly higher than the current state of the art. “What slows them down is its layer-per-layer powder deposition, typically just 20 to 100 micrometres at a time. We don’t do this. Therefore, we can obtain speeds similar to automatic welding which is over ten times faster,” Galle points out. “Thin layers are beneficial for fine details but are a waste of time for the sections of the objects on which high precision is not required. In addition, current printing methods require post-processing, like support removal, threading or smooth finishing. However, the lion’s share of production companies is not interested in such high precision on the entire part. To improve its speed, ValCUN lets its printers add the finishing tools such that post-production time can be reduced. Since the parts aren’t surrounded by unused metal powder, it is easier to sand or mill off the rough edges or faces in the same device while the rest of the object is still being printed. This way, when you take your object out of the machine, it can be entirely finished. Therefore, the industry is better off with our faster and more economical alternative.”
Small-medium corporations and hobbyists
Though their technology is still in development, a share of companies already see opportunities in a collaboration with ValCUN. Especially for the creation of parts that eject heat, the technology is highly anticipated. “In industries like plastic moulding, dissipating the heat generated in the process is vital. The quicker you get rid of it, the more profitable your production line becomes. Since aluminium is very conductive, it is highly suitable. The same applies for the creation of heat sinks for electronic devices, power electronics and battery packs for, among other things, electric cars. By printing these items, companies will be able to work faster and at lower costs than they can even imagine today.”
The first printer ValCUN will produce will have a price tag of around 50,000 euros, well below the 200,000 to one million euros you pay for today’s technology. The ambition, however, is to drive down this price throughout time and, eventually, offer a basic model for about 5,000 euros. “This way, we reach the initial goal I had in mind while building my rocket engine: making metal additive manufacturing affordable for hobbyists and medium to small corporations and welcoming them into the future of production.”
Subscribe to Our Newsletter
Receive our monthly newsletter by email